How fulfilment warehouses handle peak season demand
Fulfilment warehouses employ dynamic strategies and advanced technologies to conquer peak seasons successfully, ensuring seamless order fulfilment even amid surging demand.
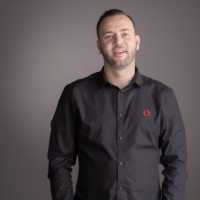
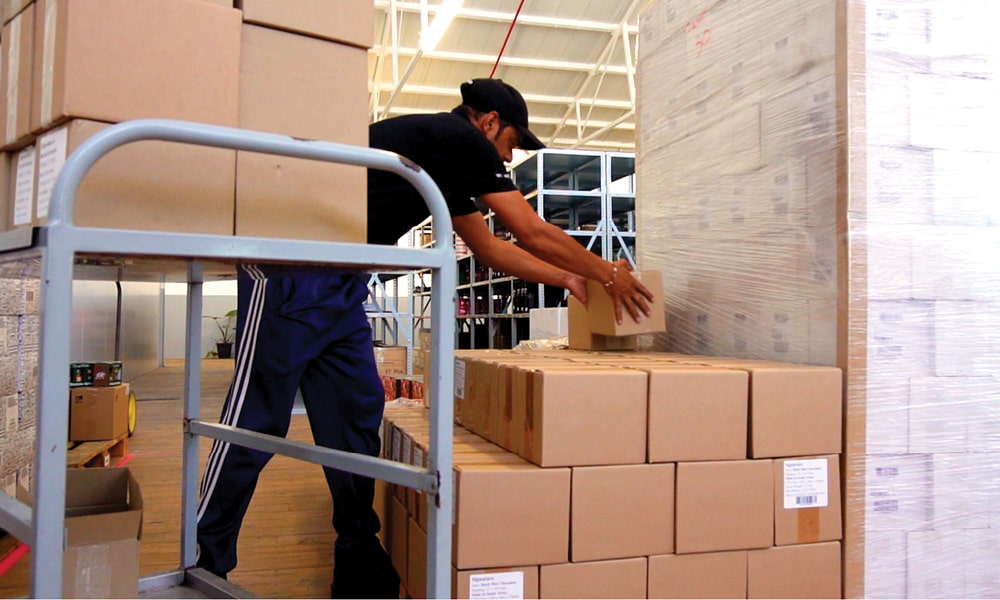
As businesses gear up for peak seasons, such as holiday periods and promotional events, the pressure on fulfilment operations reaches its zenith. The ability to efficiently handle high demand during these peak times is crucial for ensuring customer satisfaction, maintaining brand reputation, and capitalising on increased sales opportunities. In this blog, we will explore the strategies employed by fulfilment warehouses to navigate peak seasons successfully, ensuring seamless order fulfilment even in the face of skyrocketing demands.
Understanding peak seasons for fulfilment centres
Peak seasons bring a surge in consumer demand, as shoppers look forward to seasonal deals and festive offers. For fulfilment centres, this means a significant increase in order volumes, challenging inventory management, and complex logistics. To meet customer expectations for timely deliveries, fulfilment centres must be well-prepared to handle the sudden surge in orders while maintaining accuracy and efficiency.
Strategies for handling high demand
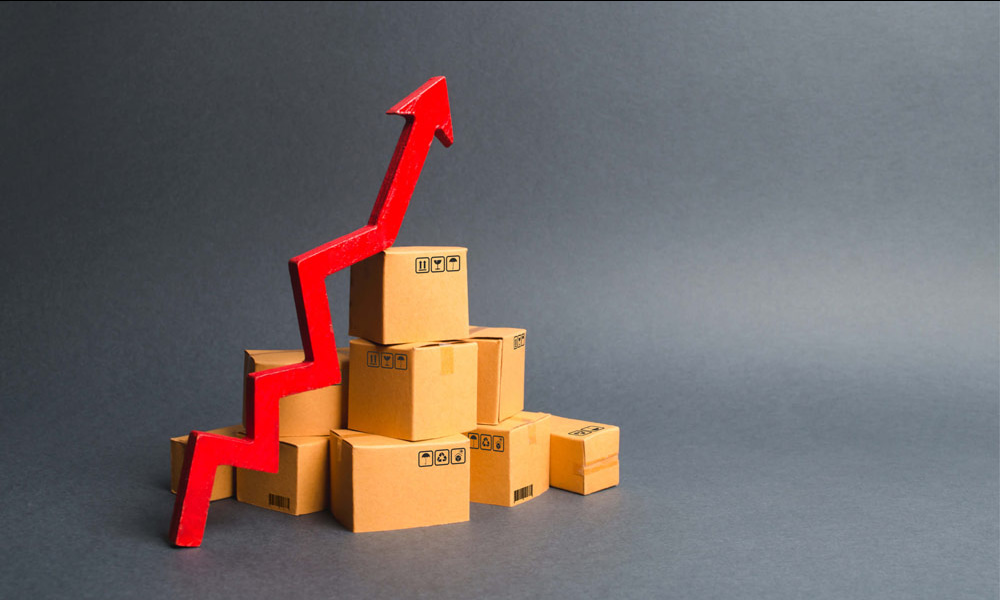
Inventory planning: Fulfilment centres utilise advanced predictive analytics to forecast demand accurately. By analysing historical data and market trends, they can optimise inventory levels, ensuring the right products are in stock when customers need them. Smart inventory planning minimises the risk of stockouts and overstocking, both of which can be costly and detrimental to customer satisfaction.
Scalable workforce: To handle the increased order volumes during peak seasons, fulfilment centres employ a flexible and scalable workforce. Temporary staff is recruited and trained in advance to support the core fulfilment team. By having a capable and well-trained workforce, fulfilment centres can ensure smooth operations without compromising on accuracy or speed.
Operational flexibility: Fulfilment centres adapt their processes and workflows to accommodate varying order sizes and handle last-minute promotions effectively. During peak seasons, there may be a higher number of rush orders or sudden changes in shipping addresses. An agile fulfilment process can handle such scenarios swiftly, ensuring on-time deliveries and minimising disruptions.
Technology integration: Automation and advanced technology play a crucial role in handling high demand efficiently. Fulfilment centres leverage robotics, conveyor systems, and automated sorting to optimise order processing speed and accuracy. Advanced software systems manage inventory levels, track shipments, and provide real-time visibility into order status, enhancing operational efficiency.
In conclusion, navigating peak seasons is a critical aspect of a fulfilment centre's operations. By employing well-crafted strategies, such as efficient inventory planning, a scalable workforce, operational flexibility, and technology integration, fulfilment warehouses can rise to the challenge of high demand.