Mastering reorder process
Essential tips to streamline your reorder process and optimise stock levels in your outsourced fulfilment warehouse.
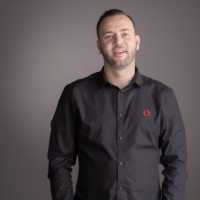
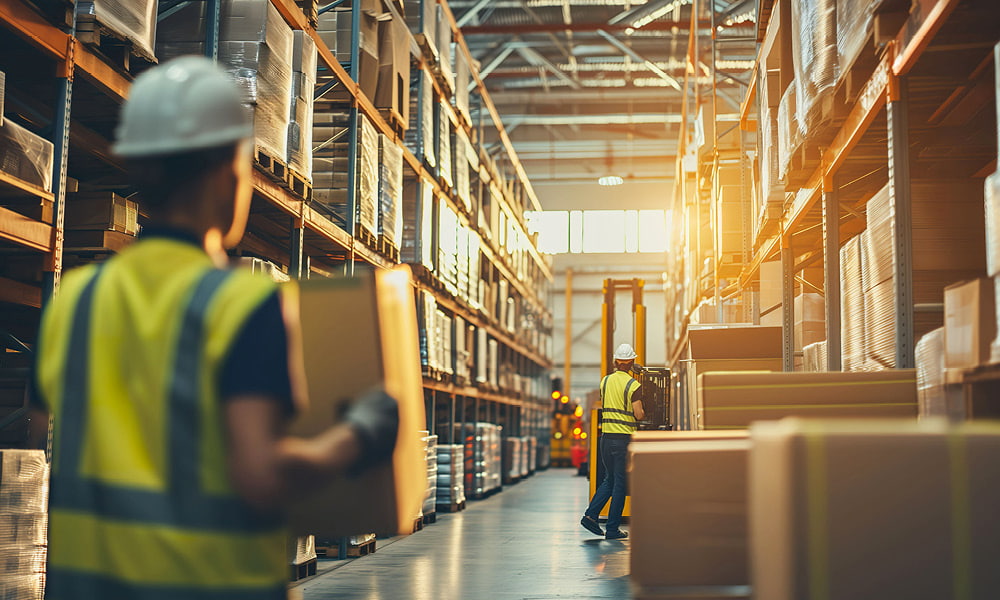
As a business that has outsourced its order fulfilment process, maintaining optimal stock levels is vital to ensure smooth and efficient operations. If you find yourself struggling with the reorder process, you're not alone.
In this blog, we will provide valuable insights and practical strategies tailored to businesses like yours, leveraging warehouse management and navigating the replenishment process seamlessly to meet customer demands without experiencing stockouts.
Set clear reorder parameters
Establish clear reorder parameters for each product in your inventory based on historical sales trends, lead times, and safety stock levels. By setting specific thresholds, you can automate the reorder process, ensuring that timely reorder requests are initiated when inventory levels approach minimum thresholds.
Collaborate with fulfilment provider
Communicate closely with your fulfilment provider to align on inventory needs and establish a collaborative reorder strategy. Share insights into sales forecasts and demand projections to help them anticipate your inventory requirements accurately. A strong partnership with your fulfilment provider ensures they can assist in timely stock replenishment, alleviating your reorder process burdens.
Leverage supplier collaboration
Strengthen relationships with your suppliers and maintain open communication channels. Share your demand forecasts with them to enable proactive planning for production and deliveries. Encouraging suppliers to provide lead time estimates can help you anticipate stock arrival and streamline the reorder process.
Review and adjust reorder frequency
Regularly review your inventory reports and reorder frequency. Analyse sales trends and customer demands to determine if your reorder parameters need adjustment. Fine-tuning your reorder frequency can help you optimise stock levels, reducing the risk of overstocking or stockouts.
Monitor inventory turnover
Keep track of inventory turnover rates to identify slow-moving products that may require special attention. Reevaluate your stocking decisions for such items and consider promotional strategies to stimulate demand and avoid carrying excess inventory.
In conclusion, these strategies will enable you to streamline the replenishment process, meet customer demands promptly, and maintain a high level of customer satisfaction. Embrace these insights, and watch your outsourced fulfilment process thrive with a well-managed reorder process and a continuous supply of inventory.